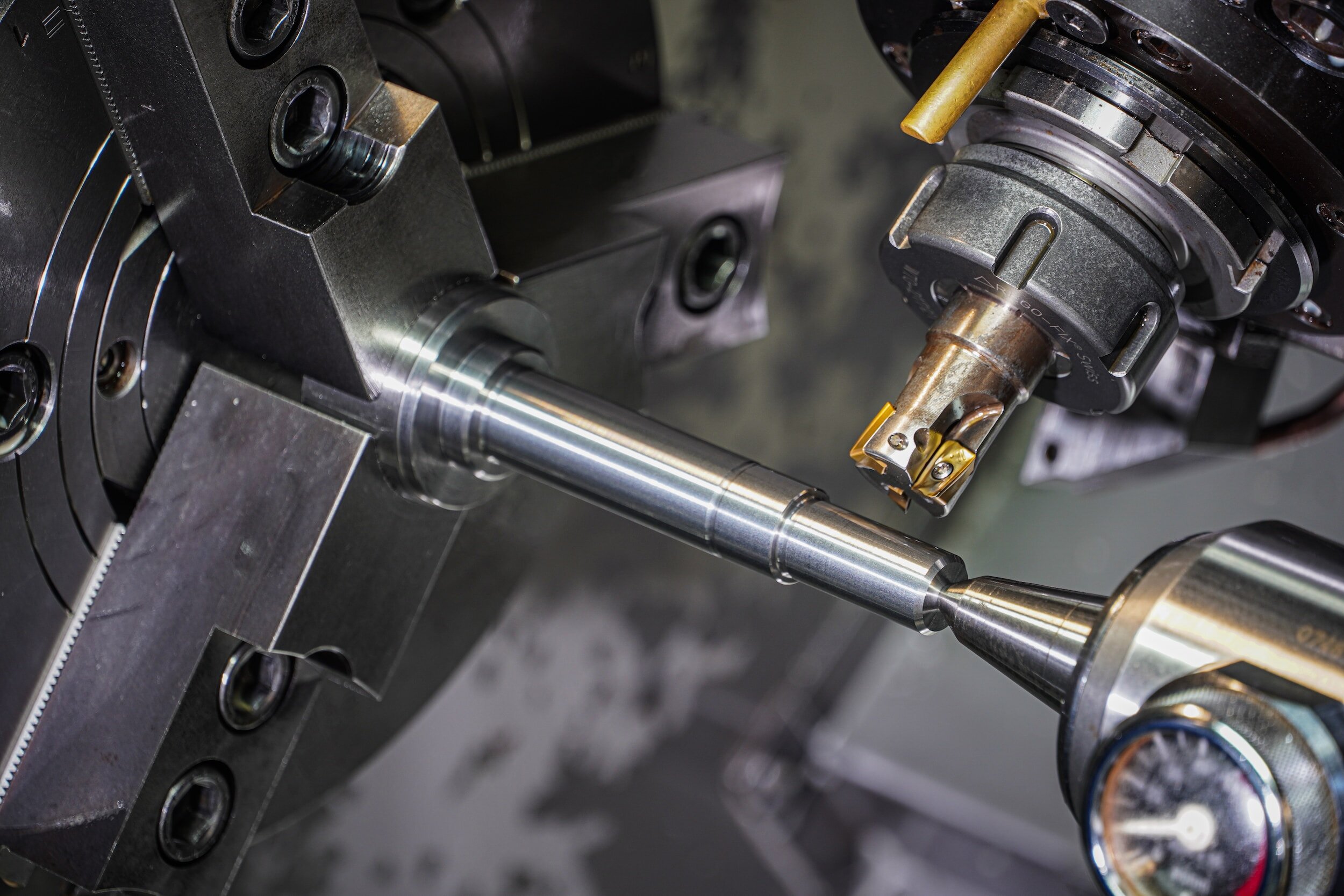
The Art of Precision Machining:
Mastering Perfection
Precision machining is a sophisticated manufacturing process utilizing computer-controlled machine tools to produce parts with exceptional accuracy.
At the forefront of precision machining, Computer Numerical Control (CNC) is a computerized manufacturing process in which pre-programmed software synchronizes and directs the movement of tools and machinery.
Together, these technologies have revolutionized the production of intricate parts, ensuring unparalleled precision, repeatability, and efficiency - key considerations of Design for Assembly.
A precision machine shop specializes in creating highly accurate and intricate components, often with the use of advanced CNC machining equipment. Shops with these capabilities can cater to critical industries including aerospace and defense, offering tailor-made solutions with exceptional precision, consistency and reliability.
Understanding Precision Machining
Precision machining has become indispensable to modern manufacturing, offering the unparalleled accuracy and consistency necessary when producing complex components at scale.
The technology is of significant value to sectors where precision is non-negotiable, such as the aerospace, medical, and automotive industries.
Precision machining allows for the creation of parts with extremely tight tolerance and intricate designs. While the process’ focus on efficiency and repeatability ensures the functionality and reliability of critical components.
Utilizing precision machining can not only enhance product quality but also the manufacturing process itself with improved efficiency and a focus on innovation through the implementation of effective Design for Manufacturing principles.
The ability to work with a diverse range of materials further underscores precision machining’s versatility, establishing it as a cornerstone of modern manufacturing.
Don’t have time to read the full guide now? Download a PDF version to read later!
A Manufacturing Tool With a Diverse Portfolio of Applications
Precision machining and CNC (Computer Numerical Control) machining have become indispensable throughout a wide range of industries, with a portfolio of applications that grows daily.
The technology’s ability to repeatedly produce highly accurate and complex components using a range of materials makes its versatility nearly limitless.
Why Has Precision Machining Become Ubiquitous Across Manufacturing?
High Accuracy and Consistency: Both techniques offer exceptional accuracy and consistency in producing parts. This precision is crucial for applications where even the slightest deviation can lead to significant performance issues or safety concerns.
Ability to Execute Complex Geometries and Intricate Designs: They can create complex shapes and intricate designs that would be difficult, if not impossible, to achieve with manual machining. This capability is essential in industries like aerospace, automotive, and medical devices, where complex components are the norm.
Material Flexibility: Precision and CNC machining can work with a vast array of materials, including metals, plastics, composites, and more. This versatility allows them to cater to the diverse needs of different industries, from electronics to construction.
Customization and Scalability: They offer high levels of customization, making them ideal for both one-off prototypes and large-scale production runs. This flexibility is beneficial for industries that require bespoke solutions or have varying production demands.
Efficiency and Speed: CNC machining, in particular, automates the manufacturing process, leading to increased efficiency and faster production times. This is crucial in industries where time-to-market is a key competitive factor.
Integration with Advanced Technologies: These machining techniques integrate well with advanced technologies like CAD (Computer-Aided Design) and CAM (Computer-Aided Manufacturing), allowing for seamless design and manufacturing processes.
Reduced Waste and Cost-Effectiveness: Precision and CNC machining are efficient in material usage, reducing waste. This efficiency, combined with the reduced need for manual labor, makes them cost-effective solutions for many industries
Industries Utilizing Precision Machining:
Aerospace
Precision machining delivers components to the aerospace industry that meet the highest standards of accuracy and reliability under extreme conditions.
Aerospace components often involve complex shapes and intricate designs. Precision machining allows for the creation of these sophisticated geometries while maintaining exacting tolerances, which is essential for components that must fit together perfectly and function reliably under extreme conditions.
The ability of precision machining to utilize and create lighter, more durable components has significantly advanced aircraft performance, safety, and fuel efficiency.
Medical
Materials used in medical devices often need to be biocompatible and have specific surface finishes to be safe for human use. Precision machining can achieve the necessary surface characteristics, such as smoothness or specific textures, which are crucial for preventing bacterial growth and reducing the risk of infection.
The versatility of precision machining allows it to handle the wide variety of materials required of the medical device and instrument industry while maintaining the integrity and functionality of the device.
Instrumentation
The role of precision machining is pivotal in ensuring that the components not only fit together perfectly but also perform their functions accurately and reliably under varying operational conditions.
The ability to work with different materials, from metals to specialized alloys, and to maintain high tolerance levels, is what makes precision machining indispensable in the manufacturing of these critical instrumentation devices.
Automotive
The engine is the heart of any vehicle, and its performance, efficiency, and reliability are crucial for the overall functioning of the car. Precision machining is essential in creating engine parts such as pistons, crankshafts, camshafts, connecting rods, and cylinder heads with exact tolerances.
Precision machining ensures that these critical parts are manufactured to the highest standards of accuracy and quality, directly impacting the vehicle's performance, longevity, and safety. This precision is also vital for newer, more advanced engines, including those used in hybrid and electric vehicles, where the demand for efficiency and reliability is even higher.
Defense
When equipping the military and armed forces even the slightest deviation in component manufacturing carries the potential to significantly impact safety and functionality.
Precision machining allows for the creation of parts with the exact tolerances required for a range of defense equipment, from firearms to advanced missile systems, ensuring the reliability and effectiveness of these products in critical situations.
Additionally, the ability to work with various materials, including advanced alloys and composites, allows the development of more durable and lightweight equipment, thereby enhancing the mobility and efficiency of defense operations.
Precision machining’s high-quality standards make it the perfect fit for meeting the stringent specifications and rigorous testing protocols of defense manufacturing.
Electronics
Precision machining is critical in the production of circuit board components, including PCB (Printed Circuit Board) housings, connectors, and heat sinks, which are fundamental to the functionality and reliability of electronic devices.
The miniaturization trend in electronics means components are becoming smaller, requiring even greater precision. Any slight deviation in dimensions can lead to electrical failures, short circuits, or inefficiencies in heat dissipation.
Precision machining also ensures the high-quality surface finishes necessary for effective soldering and electrical conductivity. Allowing for the machining of various materials used in electronics, such as copper, aluminum, and various alloys, with the precision required for efficient and reliable electronic performance.
In an industry where technological advancements are rapid and component sizes are continually shrinking, the role of precision machining in ensuring the accuracy and functionality of circuit board components is paramount.
Cutting-Edge Technology in Precision Machining: State-of-the-Art Machine Shop Facilities in 2023
In 2023, a state-of-the-art precision machine shop is a nexus of innovation and efficiency. Here's what customers can expect from these advanced facilities in today's fast-evolving industrial landscape:
Advanced CNC Equipment
Expect to find the latest Computer Numerical Control (CNC) machines, offering unparalleled precision and efficiency. These machines can handle complex tasks with high accuracy, essential for modern manufacturing demands.
3- or 5-Axis Machining Capabilities
A top-tier shop will feature either 3- or 5-axis machining technology, allowing for intricate and multidimensional cutting with exceptional detail, vital for advanced manufacturing sectors.
Comprehensive Material Handling
Diverse Material Expertise
State-of-the-art shops are equipped to work with a wide range of materials, from metals like titanium and aluminum to advanced composites and plastics, catering to various industry needs.
Material Optimization Techniques
Advanced material handling techniques ensure optimal use of resources, reducing waste and enhancing the strength and durability of the machined parts.
Precision and Quality Assurance
High Precision Tools and Equipment
Expect high-precision tools that deliver exact tolerances, crucial for industries where minute details matter, like aerospace and medical device manufacturing.
Stringent Quality Control Processes
These shops implement rigorous quality control measures, including dimensional inspection and surface finish analysis, ensuring every component meets the highest standards.
Customization and Flexibility
Tailored Manufacturing Solutions
A modern precision machine shop offers customized solutions, adapting to unique project requirements and providing bespoke manufacturing services.
Rapid Prototyping Services
With capabilities like 3D printing and rapid prototyping, these shops can quickly turn designs into functional prototypes, accelerating the development process.
Advanced Software Integration
Sophisticated Design and Simulation Software
State-of-the-art shops utilize advanced CAD/CAM software for precise design and simulation, ensuring flawless execution from concept to final product.
Industry 4.0 Integration
Expect integration with Industry 4.0 technologies, enabling smart manufacturing practices like real-time monitoring and predictive maintenance for enhanced efficiency.
In 2023, a state-of-the-art precision machine shop is not just about cutting and shaping materials; it's a hub of technological innovation, material expertise, and customized solutions, all geared toward meeting the exacting demands of modern industries.
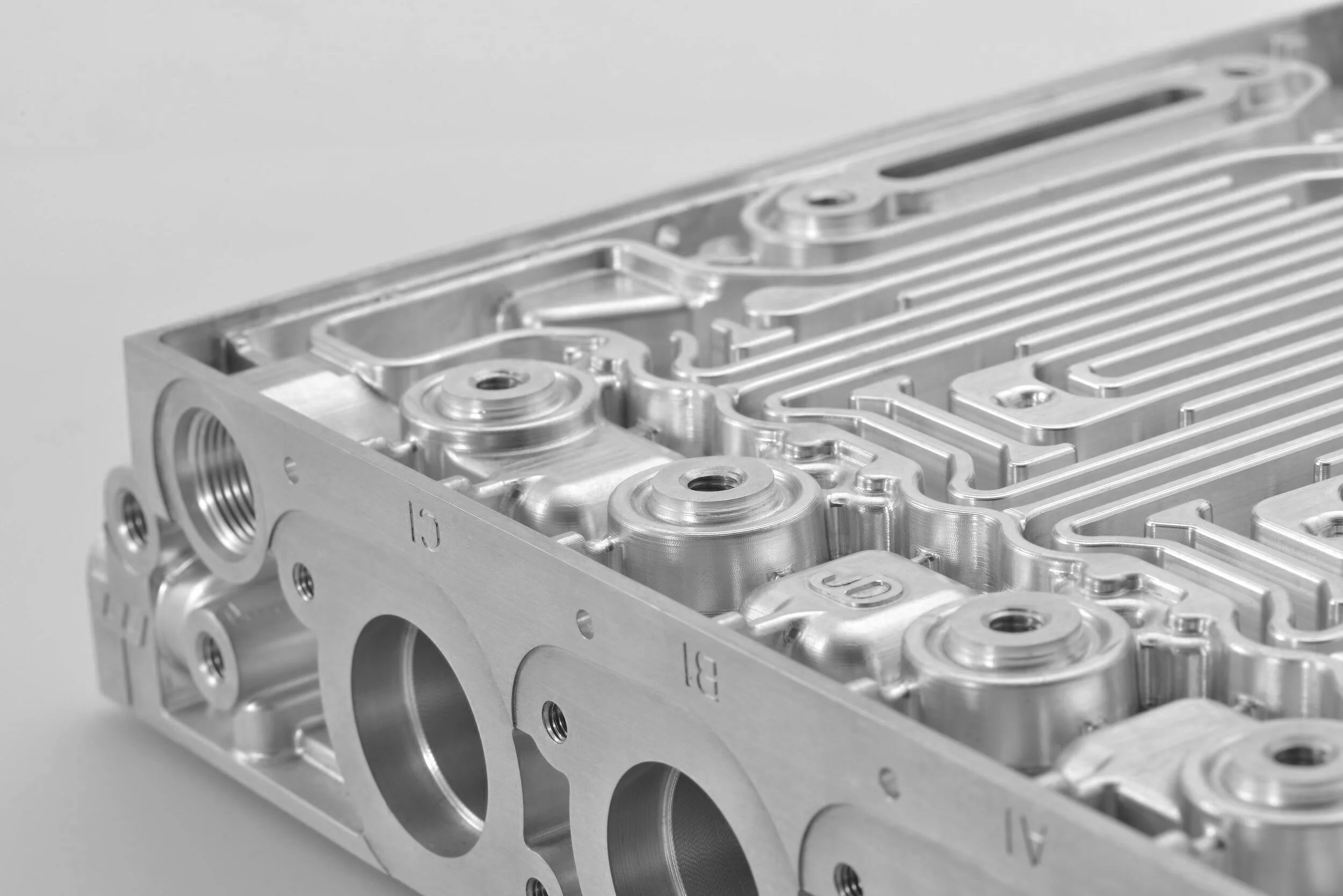
Understanding CNC Machining: A Modern Manufacturing Marvel
CNC (Computer Numerical Control) machining is a highly precise and automated process used in manufacturing to control machine tools with computer programming. This technology has revolutionized the way we create parts and components across various industries.
How CNC Machining Works
CNC machines operate based on CAD (Computer-Aided Design) and CAM (Computer-Aided Manufacturing) software. These programs convert digital designs into numerical codes, guiding the machine's movements to cut and shape material into final products with exceptional accuracy.
Key Features of CNC Machining
Precision and Consistency
CNC machining stands out for its ability to produce parts with extremely tight tolerances, ensuring consistent quality even in high-volume production runs. This precision is crucial in industries like aerospace, automotive, and medical devices.
Increased Efficiency and Productivity
Automated CNC machines significantly reduce manual labor and increase production speed, leading to higher efficiency and productivity in manufacturing processes.
Reduced Waste
With precise cutting and material usage, CNC machining minimizes waste, making it a cost-effective solution for both small and large-scale production.
In summary, CNC machining represents a cornerstone of modern manufacturing, offering precision, versatility, and efficiency. Its ability to adapt to various materials and complex designs makes it an invaluable asset in today's industrial world.
Versatility in Materials and Applications
CNC machines can work with a diverse range of materials, including metals, plastics, and composites. This versatility makes them suitable for a wide array of applications, from simple parts to complex components with intricate geometries.
Advantages of CNC Machining
Flexibility and Customization
CNC machining offers unparalleled flexibility in manufacturing, allowing for easy customization and rapid adjustments to meet specific design requirements.
The Future of Precision Machining: Innovations and Trends
This field of precision manufacturing is set for transformative changes, driven by technological advancements and new industry demands.
Here's a glimpse into what we think might lie ahead:
Emerging Technologies in Precision Machining
The future of precision machining is poised to be shaped by cutting-edge technologies. Advancements in AI and machine learning are expected to bring about smarter, more autonomous CNC machines capable of self-optimization and predictive maintenance.
Integration of Additive Manufacturing
Additive manufacturing, or 3D printing, is set to play a significant role in the future of precision machining. This integration will allow for more complex geometries and the creation of parts that are lighter yet stronger, revolutionizing design possibilities.
Enhanced Material Capabilities
Advancements in Material Science
The development of new, high-performance materials will expand the capabilities of precision machining. Expect to see more use of composites and advanced alloys, offering improved strength, durability, and heat resistance.
Sustainability in Material Usage
Sustainability will become a key focus, with precision machining adopting more eco-friendly practices. This includes recycling materials and optimizing processes to reduce waste and energy consumption.
Automation and Efficiency
Increased Automation and Efficiency
Automation will continue to advance, with machines becoming more efficient and less reliant on human intervention. This will lead to faster production times, reduced errors, and lower costs.
Customization and Flexibility
The demand for customization will drive the development of more flexible machining processes. Precision machining will need to adapt quickly to changing designs and small-batch production without sacrificing quality or efficiency.
The future of precision machining is set to be dynamic and innovative. With technological advancements, sustainable practices, and increased automation, the industry will continue to evolve, offering more efficient, accurate, and versatile machining solutions.
Corbett Engineering. A Leader in Precision Machining Thought and Practice.
At the forefront of a revolution in precision machining, Corbett Engineering's state-of-the-art machine shop embodies the future of this dynamic field. Embracing groundbreaking technologies such as AI, advanced material science, and the integration of additive manufacturing with traditional techniques, we are redefining the possibilities in precision machining. This evolution promises enhanced efficiency, greater customization, and sustainable manufacturing practices.
As a leader in this industrial transformation, Corbett Engineering is not just a service provider but a partner in innovation. Our facility is equipped with the latest CNC technology, adept at handling complex and intricate designs across various industries, including aerospace, automotive, and medical. Our expert team continually explores new materials and methods, ensuring top-tier quality and performance.
Understanding that each business has unique needs, we offer customized solutions, tailored to specific requirements. Our approach is collaborative, focusing on improving efficiency, reducing costs, and driving product innovation for our clients. In an era where precision machining is rapidly evolving, partnering with Corbett Engineering means staying ahead in the industry. Let's shape the future together, with precision at its core.