
Design for Manufacturability:
Creating Products for Efficient Production
Design for Manufacturability (DFM) is a fundamental approach in product development that focuses on designing products to optimize their manufacturability, cost-effectiveness, and overall efficiency during manufacturing.
DFM aims to create products that can be produced with minimal complexity, reduced production costs, and improved quality. This pillar page explores the key concepts, benefits, strategies, and best practices of Design for Manufacturability.
Introduction to Design for Manufacturability
Design for Manufacturability (DFM) is a systematic approach to product design that focuses on creating products with the primary consideration of their ease of manufacturing. It involves designing products to optimize production efficiency, reduce manufacturing costs, and minimize potential challenges during the manufacturing process. DFM considers factors such as material selection, manufacturing processes, assembly methods, and overall production constraints.
The importance of DFM lies in its ability to bridge the gap between design and manufacturing, ultimately leading to better products and streamlined production processes. Companies can achieve several key advantages by integrating manufacturing considerations during the design phase.
The evolution of Design for Manufacturability (DFM) is closely tied to the historical development of manufacturing processes, technological advancements, and changing market demands. Over the years, DFM has emerged as a pivotal strategy in product design, driven by the need for efficiency, cost-effectiveness, and quality in manufacturing.
Don’t have time to read the full guide now? Download a PDF version to read later!
Early Industrial Revolution (18th to 19th Century):
The concept of DFM traces back to the Industrial Revolution when mechanization and mass production techniques began to reshape manufacturing. During this period, the focus was primarily on improving production efficiency through standardization and mechanization of processes.
World War II and Post-War Period:
The mid-20th century marked a significant shift in manufacturing as industries geared up for war efforts. Mass production techniques became more refined, but complexity increased due to the demands of advanced weaponry. Post-war, manufacturers sought ways to streamline production while maintaining quality and minimizing costs, giving rise to the foundation of modern DFM principles.
1960s-1970s:
Complex designs often lead to intricate manufacturing processes. Our engineers work to simplify designs where possible, reducing the need for specialized tooling and processes.
1980s-1990s:
The 1980s witnessed a surge in global competition, which led manufacturers to seek innovative ways to stay competitive. This era saw the formalization of DFM principles as a strategic approach. Companies began integrating design and manufacturing departments to foster collaboration and ensure that designs were manufacturable.
Late 1990s-Present:
The rise of globalization and the digital age further accelerated the evolution of DFM. Supply chains became more intricate, and companies started considering the impact of design decisions on the entire product lifecycle, including production, distribution, use, and disposal. Materials science, simulation technology, and automation advancements have continued to shape DFM practices.
Current and Future Trends:
In the present day, DFM is about optimizing traditional manufacturing processes and leveraging emerging technologies. Concepts such as additive manufacturing (3D printing), the Internet of Things (IoT), and artificial intelligence (AI) are influencing the way products are designed and manufactured. These trends shift the focus toward customization, sustainability, and highly efficient production processes.
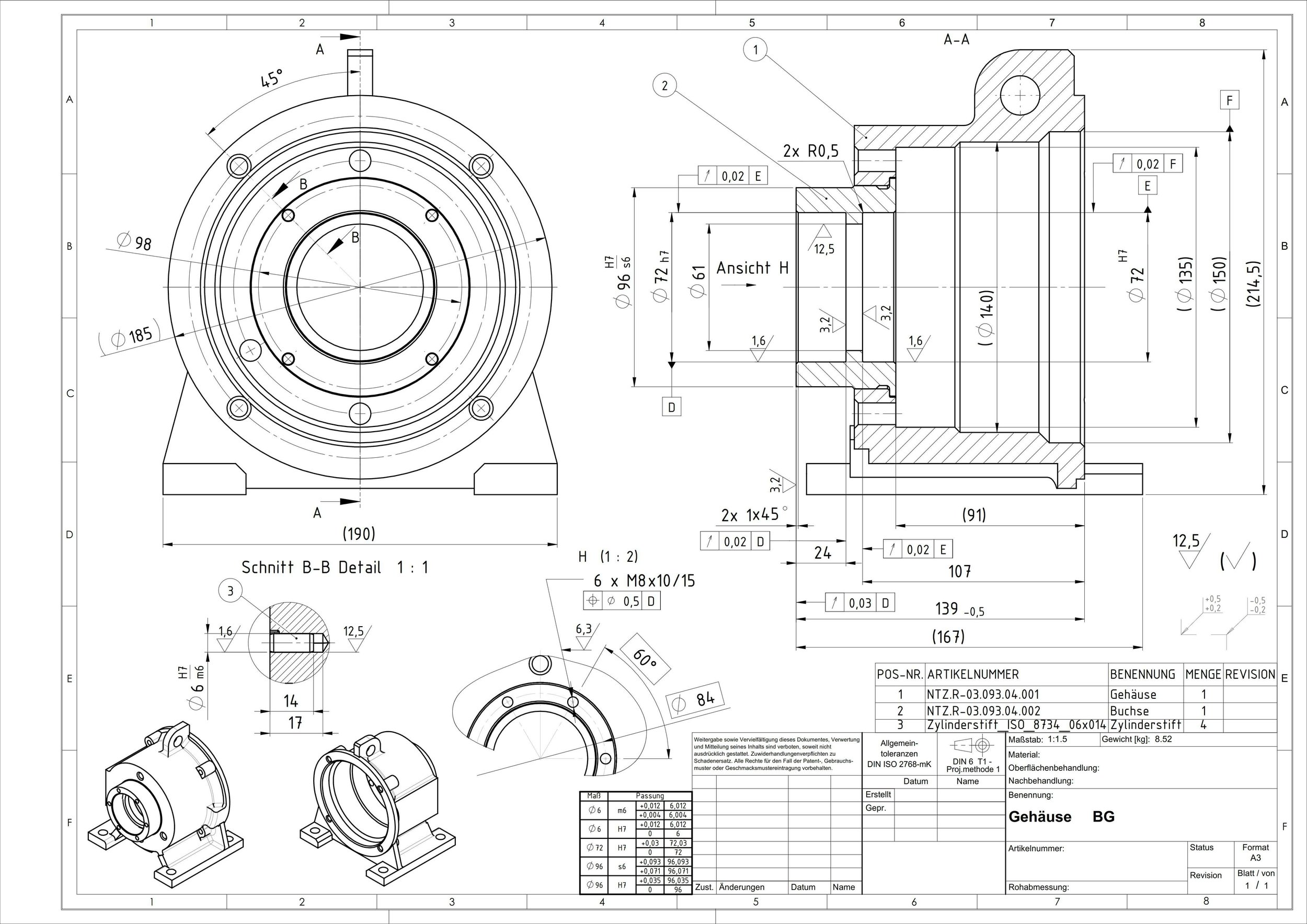
Benefits of Design for Manufacturability
By prioritizing manufacturability during the design phase, companies can unlock significant advantages across cost, time-to-market, quality, sustainability, and more.
Here, we delve into the key benefits that DFM offers:
1. Reduced Production Costs:
DFM's primary advantage lies in its potential to reduce production costs. By designing products with manufacturing efficiency in mind, companies can minimize complexities in assembly, reduce the need for specialized tooling, and optimize production layouts. Simplified designs lead to faster manufacturing processes, lower labor costs, and decreased waste, contributing to overall cost savings.
2. Faster Time-to-Market:
DFM expedites the transition from design to production. When plans are aligned with manufacturing capabilities, fewer design iterations are required during the production phase. This streamlined approach accelerates the production ramp-up, allowing companies to introduce new products to the market faster, capitalizing on competitive opportunities and capturing consumer demand.
3. Enhanced Product Quality:
DFM encourages identifying and resolving potential manufacturing challenges early in the design process. Addressing these challenges preemptively results in products that are less prone to defects, inconsistencies, and assembly errors. This focus on quality contributes to improved customer satisfaction, reduced returns, and a more substantial reputation in the marketplace.
4. Improved Sustainability:
Design choices significantly impact a product's environmental footprint. DFM promotes sustainable practices during the design phase by considering material selection, waste reduction, and energy consumption. By creating products optimized for efficient production and minimizing resource use, companies contribute to eco-friendly manufacturing and align with global sustainability goals.
5. Enhanced Collaboration:
Implementing DFM necessitates cross-functional collaboration between design, engineering, and manufacturing teams. This collaborative approach fosters a deeper understanding of the product's lifecycle and ensures that all perspectives are considered. Effective team communication results in more informed design decisions, fewer conflicts during production, and a more seamless development process.
6. Streamlined Supply Chain:
DFM principles often emphasize standardization and modular design, which facilitate using standard components across multiple products. This approach simplifies inventory management and reduces the complexity of the supply chain. Suppliers benefit from producing standardized components, leading to cost savings through economies of scale.
7. Flexibility for Customization:
DFM does not imply sacrificing product innovation or customization. Instead, it encourages designs adapted for variations without overcomplicating manufacturing processes. This flexibility enables companies to respond quickly to market demands and offer personalized product options to customers.
8. Competitive Advantage:
Companies that embrace DFM gain a competitive edge by producing high-quality, cost-effective products faster than their counterparts. The ability to consistently deliver well-designed products resonates with customers and cultivates brand loyalty. Moreover, reduced costs allow for competitive pricing, positioning the company favorably in the market.
9. Minimized Risk:
DFM helps mitigate risks associated with production delays, defects, and cost overruns. Early identification and resolution of design-related manufacturing issues reduce the likelihood of disruptions during production. This proactive risk management approach safeguards project timelines and financial outcomes.
Key Concepts in Design for Manufacturability
DFM is applied during the design phase to ensure the product is straightforward, reducing manufacturing costs and complexity. Below are some of the key concepts that form the backbone of DFM.
Simplicity
One of the fundamental principles of DFM is to simplify the product design as much as possible. This might include reducing the number of parts, using standard components, or designing multifunctional pieces that serve multiple purposes. A more straightforward design often leads to fewer steps in the assembly process and less room for error.
Standardization
Using standard parts and materials wherever possible can significantly reduce manufacturing costs. Standardized components are usually more readily available and less expensive than custom parts. This also simplifies inventory management and can speed up the manufacturing process.
Modular Design
Modular design involves creating interchangeable parts in various configurations or products. This can make manufacturing more flexible and reduce costs, as fewer unique parts must be produced and stored.
Minimize Fasteners and Assembly Steps
Each additional screw, bolt, or welding operation adds to the manufacturing cost and time. By designing products that snap-fit together or otherwise minimize the need for other fasteners and procedures, you can reduce the cost of both the parts and the labor required for assembly.
Self-Locating and Self-Fastening Parts
Designing parts that naturally align into the correct position without requiring manual adjustment can significantly speed up the assembly process and reduce the risk of errors.
Tolerance Analysis
Maintaining strict tolerances can be expensive. Manufacturers often achieve significant cost savings by relaxing tolerances without affecting product quality. Tolerance analysis ensures that parts fit together correctly, even if not manufactured perfectly.
Material Considerations
The choice of materials can significantly impact manufacturing efficiency. Materials should be chosen not only for their suitability for the end use but also for their ease of processing. Some materials are more accessible to cut, mold, or weld than others, affecting the overall manufacturability of the product.
Process Capability
Understanding the capabilities and limitations of your manufacturing processes is crucial. Designs should be tailored to the strengths of the available machinery and equipment. This helps avoid expensive custom solutions for manufacturing problems that could have been avoided during the design stage.
Error-Proofing
Incorporating features that make it impossible to assemble the product incorrectly can save time and reduce waste. This concept, also known as "poka-yoke" in Lean Manufacturing, helps to prevent errors before they occur.
Design for Automation
As manufacturing becomes increasingly automated, designs should facilitate easy handling and assembly by machines. This might involve adding features that make it easier for robotic arms to grasp a part or designing components so they can only be inserted in the correct orientation.
By incorporating these and other DFM principles into the product design process, companies can achieve substantial cost savings, increase manufacturing efficiency, and bring products to market more quickly.
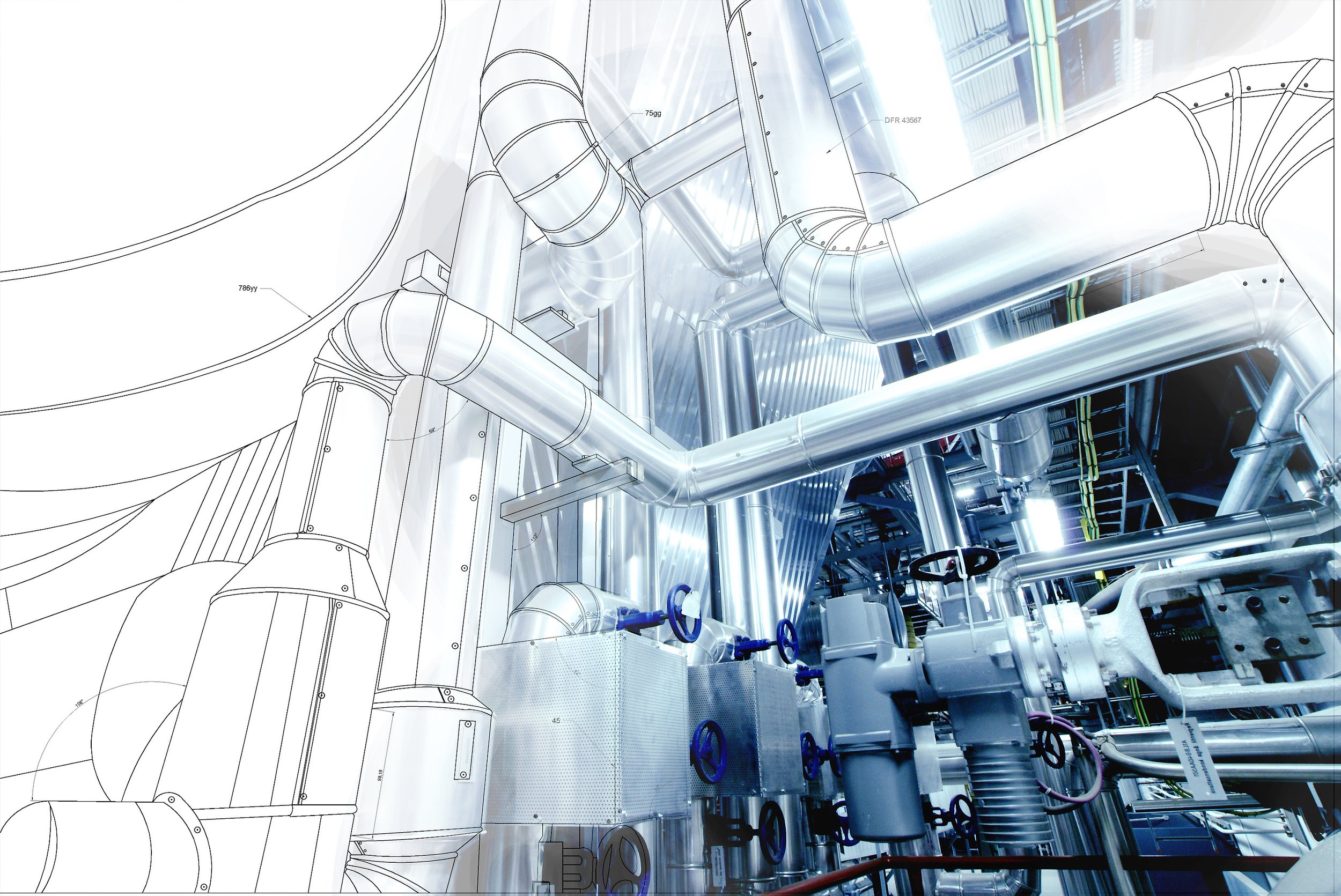
Strategies for Implementing DFM
Implementing Design for Manufacturability (DFM) can seem daunting, but when approached with systematic strategies, it can yield substantial benefits, including cost savings, improved product quality, and faster time-to-market. Here are some strategies to effectively implement DFM in your organization:
1. Cross-Functional Teams
DFM cannot be the sole responsibility of the design or engineering department. A cross-functional team comprising design, engineering, manufacturing, and quality assurance members can provide a well-rounded perspective on what is realistically manufactured. Regular meetings should be held to discuss DFM considerations and ensure everyone is aligned with these objectives.
2. Early Involvement
DFM considerations should be brought into the product development as early as possible. This ensures that the design evolves with manufacturability in mind, reducing costly revisions later. Early-stage DFM assessments can involve basic calculations and heuristic methods, but they set the stage for more detailed analyses as the design matures.
3. Continuous Training
Continuous training programs can keep the design and manufacturing teams updated with the latest DFM techniques and tools. Training can range from workshops to courses and can even be a part of the organization’s knowledge-sharing platform. This helps in institutionalizing DFM as a part of the organizational culture.
4. Use of Software Tools
There are specialized software tools available that can assist designers in evaluating the manufacturability of their designs. These tools offer real-time feedback and can often integrate with existing CAD software. They can highlight issues like difficult-to-machine geometries, suggest more readily available standard components, or recommend adjustments to meet the tolerance capabilities of the general manufacturing processes.
5. Guidelines and Checklists
Creating internal DFM guidelines and checklists can be a practical way to help designers consider manufacturability aspects systematically. These should be easy to follow and cover significant points of concern, such as materials, part count, assembly considerations, and process capabilities.
6. Prototyping and Testing
Virtual prototyping and simulation can be great tools for initial DFM evaluation. However, they should be complemented by creating physical prototypes to understand real-world manufacturing challenges. Prototyping feedback should be integrated into the design to improve it further.
7. Feedback Loops
Create a system where feedback from the manufacturing floor flows back to the design team. This feedback can be invaluable for highlighting unforeseen challenges and opportunities for design improvement. Lessons learned from one project should be documented and applied to future endeavors.
8. Cost-Benefit Analysis
DFM should be approached as an investment. Every recommended change should undergo a cost-benefit analysis to determine its viability. The long-term benefits, such as reduced manufacturing costs and increased product quality, should be weighed against the short-term costs of implementing DFM strategies.
9. Vendor Collaboration
If your manufacturing is outsourced, it’s crucial to collaborate with your vendors on DFM initiatives. They have firsthand knowledge of what can and can’t be done efficiently with their equipment and can provide valuable suggestions for design improvement.
10. Metrics and KPIs
Finally, set metrics and Key Performance Indicators (KPIs) to track the success of your DFM implementation—these range from reduced production costs and time to increased product quality and customer satisfaction.
Through these strategies, a DFM approach can become an integral part of your product development lifecycle, leading to products that meet customer expectations and are more accessible and more cost-effective to produce.
Best Practices for Design for Manufacturability
Incorporating Design for Manufacturability into your product development cycle can yield remarkable advantages, including reduced production costs, faster lead times, and improved product quality. To realize these benefits, certain best practices should be observed.
Engage Early and Collaborate
The earlier DFM is integrated into the design process, the better. Designers should consult with engineers, manufacturers, and even suppliers from the inception of a product. This collaboration ensures the design is optimized for materials, tooling, and production processes. Late-stage design changes are costly and delay production, so it is crucial to get it right from the start.
Set Clear Objectives
Prioritize what you aim to achieve with DFM—reducing costs, simplifying assembly, or shortening the production cycle. Clear objectives will help guide design decisions and facilitate effective cross-functional teamwork.
Use Standard Parts and Materials
Leveraging standard off-the-shelf components can significantly reduce both lead time and cost. Custom parts often require specialized tooling and longer lead times, which can delay production and increase costs. Furthermore, standard components are typically easier to source and have known performance characteristics.
Minimize Part Count
One of the primary goals of DFM is to simplify product structures to use the fewest parts possible. Each additional piece adds complexity, cost, and other points of failure to the assembly process. Simplifying designs often reduce labor costs, faster assembly times, and less room for error.
Optimize Design for Specific Manufacturing Techniques
Every manufacturing process—be it injection molding, CNC machining, or additive manufacturing—has its own set of guidelines for optimal design. For example, consider factors like wall thickness, draft angles, and gate locations if you are designing a part for injection molding. Tailoring your design to the strengths and limitations of the manufacturing process will result in more efficient and cost-effective production.
Consider Tolerances Carefully
While it might be tempting to specify tight tolerances across the board to ensure high-quality products, it can drastically increase costs. Use tolerances as loose as possible while still meeting functional requirements to facilitate more accessible, more cost-effective manufacturing.
Design for Easy Assembly
Parts should be easy to align and assemble without requiring specialized tools or equipment. Self-locating and self-fastening designs can significantly reduce assembly time and minimize the chance of incorrect assembly.
Validate with Prototypes
Use prototypes to validate that your designs are functional and manufacturable. Physical prototypes allow you to assess assembly, fit, and function easily. Any issues can be addressed in the plan before production, avoiding costly modifications to tooling and processes.
Iterate and Refine
After receiving feedback from the manufacturing and assembly teams, use this information for continuous improvement. Lessons learned should be documented and applied to future projects to develop a culture of excellence in design for manufacturability.
Keep Documentation Updated
Thorough, accurate documentation can make the manufacturing process smoother and more efficient. Ensure design changes are reflected in associated documents and easily accessible to all relevant departments.
By following these best practices, your organization can optimize designs for easier, more efficient, and cost-effective manufacturing, thus realizing DFM's full benefits.
Case Studies and Real-World Examples
Apple's Design Principles for Manufacturability
Apple's design principles for manufacturability epitomize the intersection of innovation and efficient production. Renowned for their sleek, functional products, Apple's approach to DFM combines aesthetics with practicality.
Central to their strategy is the pursuit of simplicity. Apple's designs often emphasize minimalistic yet elegant forms that reduce manufacturing complexity. Fewer components and straightforward assembly processes not only streamline production but also enhance product reliability.
Material selection plays a pivotal role. Apple opts for readily available materials that meet strict quality standards and can be efficiently sourced. This approach not only supports consistency in production but also aids in cost management.
Precision is another hallmark. While embracing design simplicity, Apple maintains a focus on precision engineering. This ensures components fit precisely and perform optimally, contributing to the overall quality and user experience.
Collaboration across design and engineering teams is a key principle. By fostering cross-functional collaboration from the outset, Apple ensures that designs align with manufacturing capabilities, reducing the need for post-design adjustments.
Apple's design principles for manufacturability demonstrate their commitment to creating products that are both visionary and practical, embodying the harmony between innovative design and efficient production processes.
Toyota's Lean Manufacturing and DFM
Toyota's remarkable success in the automotive industry is not solely attributed to the quality of their vehicles but also to their revolutionary manufacturing approach known as Lean Manufacturing. Coupled with their dedication to Design for Manufacturability (DFM), Toyota has set industry standards that prioritize efficiency, quality, and innovation.
Toyota's Lean Manufacturing, inspired by the Toyota Production System (TPS), aims to eliminate waste in all its forms, from excess inventory to inefficient processes. This approach streamlines production, minimizes costs, and enhances quality. Key principles include:
Just-In-Time Production: Toyota's assembly lines operate on a "pull" system, ensuring that parts are delivered only when needed. This reduces inventory costs and prevents overproduction.
Continuous Improvement (Kaizen): Toyota's commitment to constant improvement encourages employees at all levels to identify and solve inefficiencies. This fosters a culture of innovation and optimization.
Elimination of Waste (Muda): Toyota identifies seven types of waste, including overproduction, defects, waiting, and unnecessary motion. By addressing these, they maximize value and minimize resource wastage.
Toyota's success doesn't end with manufacturing—it starts with design. DFM at Toyota emphasizes seamless integration between design and manufacturing teams. Key aspects include:
Simplicity and Standardization: Toyota focuses on designs that prioritize simplicity, making production processes smoother and more efficient. Standardized components across different models reduce complexity.
Early Collaboration: Toyota's design and manufacturing teams work closely from the outset. This minimizes late-stage design changes, avoiding costly disruptions during production.
Error Prevention: Toyota designs products with an eye toward preventing errors. This proactive approach reduces defects and maintains consistency in quality.
The synergy between Lean Manufacturing and DFM at Toyota is a testament to their commitment to holistic excellence. By eliminating waste, optimizing processes, and designing for efficient production, Toyota has set a benchmark for the industry. The combination of Lean principles and DFM ensures that Toyota's vehicles not only delight customers but also uphold the highest standards of quality and efficiency from concept to creation.
Boeing's Aerospace Innovations in DFM
Boeing, a pioneering force in the aerospace industry, has consistently demonstrated innovative approaches to Design for Manufacturability (DFM), reshaping aircraft production and design processes.
Boeing's DFM innovations are driven by a relentless pursuit of efficiency, quality, and performance:
Advanced Materials: Boeing has pioneered the use of advanced materials like carbon composites in aircraft construction. These materials offer both weight reduction and increased strength, resulting in more fuel-efficient and agile aircraft.
Digital Design and Simulation: Boeing employs cutting-edge digital tools and simulation techniques to virtually test and optimize designs before physical production begins. This approach reduces the need for costly physical prototypes and minimizes design changes during manufacturing.
Modular Design: Boeing's modular design approach allows different sections of an aircraft to be manufactured concurrently and assembled seamlessly. This accelerates production while maintaining stringent quality standards.
Automated Manufacturing: Boeing has integrated automation into its manufacturing processes, from robotic assembly to 3D printing of components. This not only improves precision but also increases production rates.
Sustainability: Boeing's DFM innovations extend to sustainability. By designing for recyclability and reduced environmental impact, they demonstrate a holistic approach to aircraft production.
Boeing's aerospace innovations in DFM underscore their commitment to pushing boundaries in aviation. By embracing advanced materials, digital tools, modular design, automation, and sustainability, Boeing has not only transformed aircraft manufacturing but also set a precedent for the industry to achieve new heights of efficiency and performance.
Challenges and Overcoming Barriers
While Design for Manufacturability (DFM) offers a host of benefits, implementing it is not without its challenges. Striking a balance between creative design and practical manufacturing considerations requires navigating potential roadblocks. Here, we explore some key challenges that arise in the realm of DFM and strategies to overcome them.
Creative Restraints:
One of the primary challenges is the perception that DFM can stifle design creativity. Designers may feel constrained by manufacturing limitations, leading to resistance in embracing DFM principles. Overcoming this challenge requires a mindset shift – understanding that DFM doesn't hinder creativity but enhances it by guiding innovation towards practical realizations.
Solution:
Education and awareness play a pivotal role here. Communicating the value of DFM in terms of optimized production processes, cost-efficiency, and improved quality can help designers appreciate its role as an enabler rather than a restraint.
Early Collaboration:
Early collaboration between design and manufacturing teams is vital for effective DFM implementation. However, different teams often have varying priorities and communication barriers can arise.
Solution:
Establishing cross-functional teams and fostering a culture of open communication are crucial. Regular meetings, workshops, and brainstorming sessions that involve both designers and manufacturing experts can bridge the gap and ensure that design decisions are well-informed by manufacturability considerations.
Balancing Innovation and Practicality:
Striking the right balance between pushing the boundaries of innovation and adhering to manufacturing practicalities can be complex. Designers may wish to introduce cutting-edge materials or intricate features that could pose challenges during production.
Solution:
This challenge can be overcome through prototyping and simulations. Creating prototypes allows designers to experiment and test the feasibility of their innovative ideas without committing to full-scale production. Digital simulations help visualize how these ideas will interact with manufacturing processes and identify potential bottlenecks.
Design Iterations:
Iterating on designs to align with DFM principles can extend project timelines and incur additional costs. Frequent design changes may disrupt the creative flow and lead to frustration.
Solution:
Integrating DFM principles into the initial design phase minimizes the need for extensive iterations later. Establishing clear DFM guidelines and involving manufacturing experts early can prevent major redesigns, reducing project delays and costs.
Resistance to Change:
Organizations with established design practices might face resistance to adopting new DFM methodologies. Changing existing workflows and mindsets can be met with resistance.
Solution:
Leadership commitment is essential for successful implementation. Showcasing success stories of organizations that have benefited from DFM can inspire confidence and motivate teams to embrace change.
Lack of Resources:
Adequate resources, including time, expertise, and technology, are necessary for successful DFM implementation. Smaller companies or those with limited budgets might struggle to allocate these resources.
Solution:
Prioritizing DFM as a strategic imperative is essential. Investing in training, tools, and technologies that support DFM can lead to substantial long-term benefits, including reduced production costs and enhanced product quality.
Balancing Trade-Offs:
DFM often involves making trade-offs between various design and manufacturing considerations. For instance, optimizing for cost might mean sacrificing certain design features.
Solution:
Decision matrices and trade-off analysis methodologies can aid in making informed choices. Cross-functional teams can collaboratively evaluate options and choose the most advantageous path forward.
Future Trends in Design for Manufacturability
Integration of AI and
Machine Learning
The integration of Artificial Intelligence (AI) and Machine Learning (ML) is revolutionizing the field of Design for Manufacturability (DFM), propelling it into a new era of efficiency and innovation. AI and ML are enhancing DFM by analyzing vast datasets, predicting manufacturing outcomes, and optimizing designs for both creativity and manufacturability.
AI-driven algorithms can simulate manufacturing processes, predict potential challenges, and recommend design modifications that optimize production efficiency. ML algorithms learn from historical manufacturing data to identify patterns, enabling designers to make informed decisions that align with successful past practices.
Moreover, AI-enabled tools offer real-time feedback during the design phase. Designers can receive instant manufacturability assessments, allowing them to iterate quickly and make adjustments to designs that might otherwise lead to production complications.
The result is a powerful synergy between human creativity and AI's computational capabilities. Integrating AI and ML in DFM fosters rapid innovation, reduced costs, and improved quality, ensuring that designs are both cutting-edge and manufacturable in a dynamic and competitive manufacturing landscape.
3D Printing and Additive Manufacturing
3D printing and additive manufacturing have emerged as transformative technologies within the realm of Design for Manufacturability (DFM). These technologies revolutionize traditional manufacturing processes by allowing for the creation of intricate, customized, and complex designs with unprecedented efficiency and precision.
One of the key advantages of 3D printing is its ability to manufacture components with minimal material waste. This aligns well with DFM principles of optimizing resource utilization and reducing environmental impact.
Additionally, additive manufacturing techniques permit designers to create geometries that were previously unattainable through conventional methods. This offers new avenues for creative design while still adhering to DFM considerations.
However, challenges such as material limitations, surface finish issues, and production speed must be addressed when integrating 3D printing into DFM. Understanding how these technologies interact with DFM principles is crucial for unlocking their full potential. As additive manufacturing continues to evolve, it presents an exciting opportunity to reimagine manufacturability and redefine the boundaries of what is possible in design and production.
Sustainable and Eco-Friendly Design
In the era of heightened environmental consciousness, the integration of sustainable and eco-friendly design practices within Design for Manufacturability (DFM) has gained significant importance. DFM strategies now extend beyond efficient production to encompass the entire lifecycle of a product, emphasizing responsible consumption, reduced waste, and lower carbon footprints.
Sustainable DFM involves selecting materials with minimal environmental impact, designing products that are easily recyclable or biodegradable, and optimizing manufacturing processes to minimize energy consumption and emissions. By considering these factors, products can be designed for longevity, circularity, and reduced environmental strain.
Eco-friendly DFM aligns with consumer preferences for ethical and sustainable products, contributing to a brand's reputation and competitive advantage. Moreover, it addresses the global imperative to combat climate change and reduce resource depletion.
While challenges like material availability, cost, and technological limitations exist, the integration of sustainable and eco-friendly principles into DFM is no longer an option but a necessity. It not only elevates product quality and marketability but also reflects a commitment to a greener future.
Conclusion
Design for Manufacturability plays a pivotal role in modern product development. By considering manufacturing processes from the outset, businesses can create products that are not only innovative but also efficient to produce. Emphasizing collaboration, simplicity, and continuous improvement, DFM sets the stage for more cost-effective, high-quality, and sustainable products.